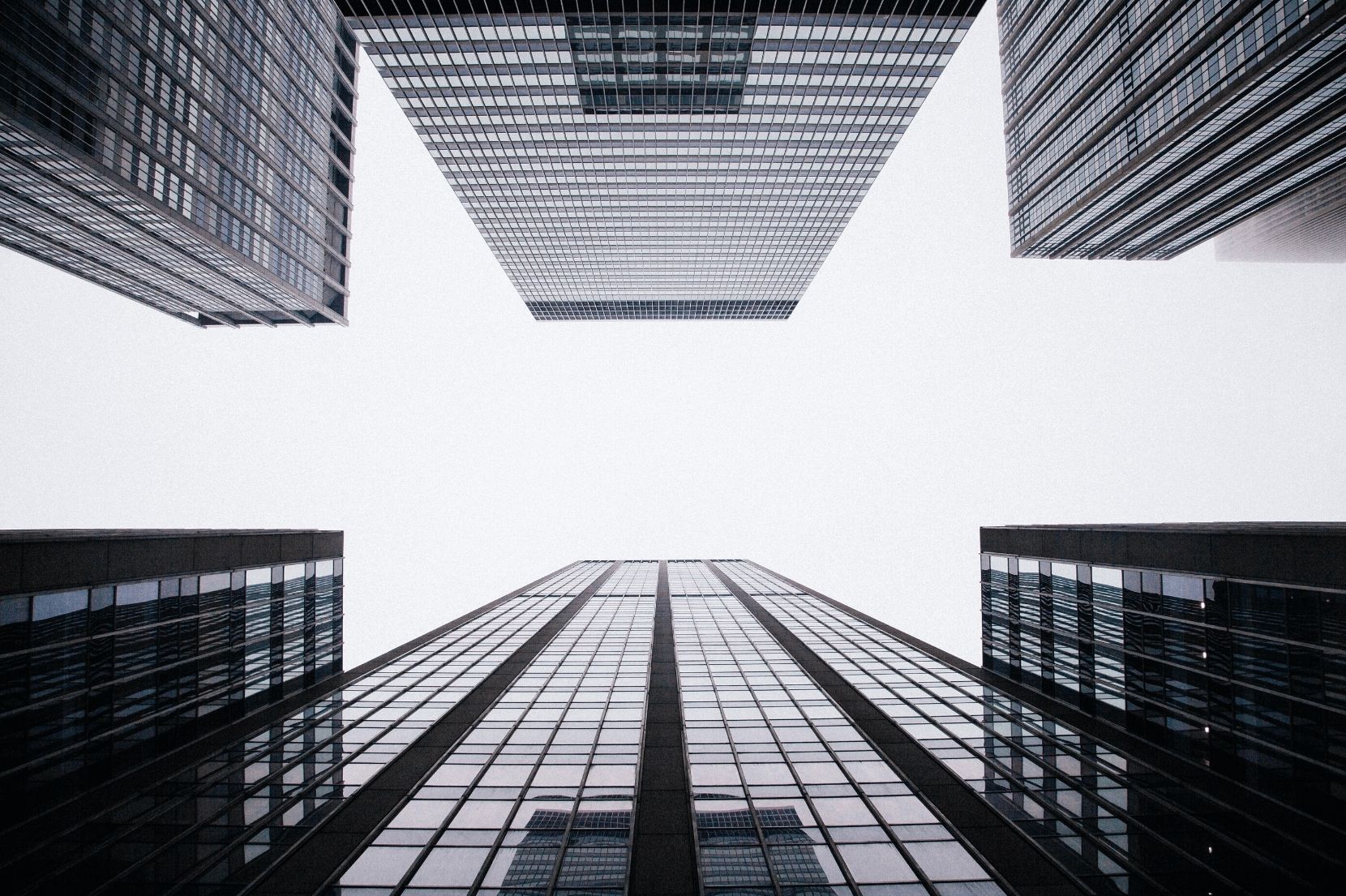
Digital Twins and Industry 4.0
Digital Twins have been positioned for several years as one of the main technologies destined to revolutionize Industry 4.0 trends. Companies from very different sectors can take advantage of Digital Twins to obtain more accurate products, reduce costs or predict possible errors.
Below, we explain what an industrial digital twin is and how to apply it to your sector through the most cutting-edge technologies of the moment.
What is a Digital Twin
Digital Twins are digital replicas of objects, spaces, physical systems, or processes. Everything is susceptible to having an artificial representation, and the digital twin is in charge of truthfully showing the operation, response, and behavior of its ‘real’ counterpart thanks to the combination of physical and virtual data.
One of its original examples was found a decade ago in NASA’s Digital Twins and the large-scale representations of its space capsules used to simulate all kinds of scenarios from a safe environment.
By using Digital Twins, companies have several benefits:
- Spend less money on product development. Checking what the final product would look like helps to anticipate potential bugs or problems that multiply the budget. It also reduces the costs of testing with physical prototypes.
- Improve the final experience of the product or service they are developing and get closer to what customers need.
- Predict the maintenance needs of the product or service once it is on the market.
How to Build a Digital Twin
To ‘manufacture’ one of these Digital Twins, one of the bases is a large amount of data, not only of the physical object but also of its environment. The more data there is, the more accurate the model will be.
For example, if we are going to create a digital twin of a building under construction, we will not only have to represent it, but also factors that influence its surroundings, such as wind speed, and the stability of the land on which it would be built or pollution levels. With this data collection, we would have a digital image that would help to build: what would be the ideal materials to build it, with what orientation to do it, what external agents could affect the facade…
The Digital Twin is visualized using 3D and Augmented Reality models. Data can be collected from previous large databases or through sensors: the expansion of the Internet of Things (IoT) helps.
Digital Twins: Applications
As we have just seen, Digital Twins are very useful for the construction sector, but they are not the only example.
A digital twin can also serve as a prototype of a physical product; it is what is known as a Digital Twin Prototype (DTP), and would serve to see, through bits, how a product works before we get our hands on it. On the other hand, the DTI (Digital Twin Instance) is a model for testing the physical product already launched.
Finally, the DTA (Digital Twin Agreggate) obtains data from the DTI that is used to improve the physical product.
In addition to the construction sector, Digital Twins can be applied in sectors such as aeronautics and aerospace: as we saw at the beginning, NASA used these models to simulate the operation of its spacecraft.
There can also be ‘human’ Digital Twins, ideal for the healthcare sector. They can be used to test operations or products before testing them on a person.
The educational sector can also use them for simulations. For example, to pilot airplanes, ships, or other means of transport.
On the other hand, the marketing departments of any company can make use of Digital Twins to show products to customers. This would give a new dimension to traditional promotional campaigns.
Digital Twins and Industry 4.0
Digital Twins and IoT
We are living a change of era with the so-called Industry 4.0. A concept driven by the use of the latest technologies and focused on generating a business culture based on continuous improvement and constant innovation. A utopian goal until the emergence of the Internet of Things or IoT, which is generating a scenario full of possibilities for all types of industries.
The incorporation of sensors in products and assets has opened up access to huge amounts of data and has created the basis for Digital Twins. In addition, technologies such as Big Data, Cloud, and Augmented or Virtual Reality have enhanced their functionalities.
Industrial Digital Twins
The connectivity of devices and sensors, homogenization, reprogramming, deployment and management of sensors or volumes of information represent the major challenges in this type of project. But these are no longer insurmountable challenges. As the Internet of Things becomes part of our environment, Digital Twins become the cornerstone of any industrial automation process.
This is the case, for example, of our collaboration with Acciona, a world leader in renewable energies, which promoted the creation of a digital twin of one of the largest solar plants in the world, with the aim of improving its efficiency and management. After developing a supervisory control and data acquisition system, we obtained real-time control of more than 48,000 alarms and 42,000 variables, which made it possible:
- Visualize the status of the systems at different levels.
- Detect any anomaly in the network.
- Be able to predict the volume of energy to be generated according to future weather.
Today, it is already possible to access a digital visualization of the detailed status of an entire plant and its component elements. It is also possible to equip the Digital Twins with Machine Learning so that they can learn and react autonomously. It is no longer a matter of collecting data. It is about managing it and learning from it.
In the scenario generated by Digital Twins, consisting of the physical world and the digital world, it is possible to analyze all kinds of data. Digital Twins integrate artificial intelligence, machine learning, advanced analytics, and spatial networks, and incorporate data obtained through the use of sensors; thereby promoting preventive/predictive maintenance and offering the possibility of testing the response of assets in scenarios of all kinds while avoiding destructive testing.
We help you to create your own Digital Twins
As you have seen in the videos above, at Plain Concepts we have organized several webinars on the advantages and challenges of Digital Twins, thanks to our experience with these tools and the technologies of Mixed Reality, Big Data, and IoT.
Now, we want to help you put them into practice in your company. We create with you the best Digital Twins to test your products.